Why Is Adhesion Important?
When it comes to pressure-sensitive labels, strong adhesion is essential for long-term performance. While label materials and adhesives are engineered to meet rigorous specifications, real-world application conditions can make or break their effectiveness.
At Weber Packaging Solutions, we’ve seen firsthand how environmental variables and application techniques can influence adhesion results. To help your team get the best performance from your labels, here are some key factors to consider.
✅5 Proven Tips
1. Apply Consistent, Firm Pressure
Pressure-sensitive labels rely on contact to bond effectively—and that starts with applying consistent, firm pressure during application.
Automated label applicators are designed to deliver this precision, and one of the most effective tools for ensuring proper pressure is a tamp pad. Tamp pads press the label directly onto the product surface with uniform force, helping eliminate air bubbles and ensuring full contact with the substrate.
Without enough pressure, labels may not fully adhere, especially along the edges, leading to issues like lifting or curling. Whether you're using a wipe-on, blow-on, or tamp application method, make sure your equipment is properly calibrated to apply sufficient force across the entire label.
❗Pro Tip: Regularly check and maintain tamp pads for wear or adhesive build-up, which can reduce application accuracy over time.
2. Prepare the Surface
Make sure the application surface is clean, dry, and free from dust, oil, or condensation. Contaminants act as a barrier between the adhesive and the surface, weakening the bond.
3. Mind the Temperature
Every adhesive has a minimum recommended application temperature. Applying labels in environments that are too cold may prevent the adhesive from activating properly, leading to adhesion failure down the line.
The average application temperature range for pressure-sensitive labels generally falls into the following categories, depending on the adhesive type:
General Purpose Adhesives- Typical Application Temperature: +40°F to +100°F (approx. +5°C to +38°C)
- Designed for standard environments and surfaces like paperboard, plastics, and metals.
- Typical Application Temperature: +20°F to +50°F (approx. –7°C to +10°C)
- Ideal for refrigerated products or cold environments like food processing plants or cold warehouses.
High-Performance Adhesives
- Typical Application Temperature: +50°F to +120°F (approx. +10°C to +49°C)
- These adhesives may bond well at higher temperatures and offer stronger performance on challenging substrates or environments (e.g., chemical drums, outdoor storage).
4. Allow the Bond to Set
Adhesive strength builds over a short bonding period. Avoid immediate rubbing, stress, or movement after application to ensure a full bond is achieved.
5. Know Your Substrate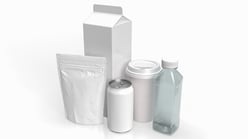
Not all surfaces are created equal. Materials like low-energy plastics, rough or textured finishes, or treated cartons may require specialized adhesives. Always check the compatibility between your label and the surface.
❗Pro Tip: Check the Technical Data Sheet
We recommend reviewing the Technical Data Sheet (TDS) for each label product. It provides detailed information on application temperatures, compatible substrates, and other essential guidance.
Need Support? We’re Here to Help.
If you experience any performance concerns with your labels, don’t hesitate to reach out. The more details you can share, such as application method, lot numbers, or photos can help us troubleshoot and resolve the issue faster.
For more information, documentation, or personalized guidance, feel free to contact our label experts.